Table of Contents
1. Introduction 2. What is an ERP System? 3. Supply Chain and Operational Benefits of ERP Systems 3.1 Integrated Systems and Streamlined Business Processes 3.2 Improved Materials Management & Production Planning 3.3 Automation of Processes 3.4 Supplier Integration 3.5 Reduced Inventory Held & Manufacturing Costs 3.6 Improved Data Accuracy 4. Potential Problems with ERP Implementations 4.1 Time & Ease of Integration 4.2 Cost/Budget 4.3 Limited Customisation 4.4 Change Management 5 Conclusion References ………………………………….…………………………………………………………………………………………..……16Introduction
This report presents an evaluation of SAP’s Enterprise Resource Planning (ERP) systems for implementation within VIVI PLC, highlighting the benefits that the company can expect in regard to improving their supply chain and logistics. After analysing the features of ERP systems, it has been identified that functionality provided within various modules such as the MM (Materials Management), PP (Production Planning) and SD (Sales & Distribution) modules, provide benefits expressed through three dimensions of Operational, Managerial and Strategic. This report also explores further by commenting how ERP implementation faces challenges such as the gap between system capabilities and business needs, data migration, data quality problems and the redesign of business processes.What is an ERP System?
Monk and Wager (2013) describes ERP systems as “core software programs used by companies to integrate and coordinate information in every area of the business. ERP programs help organisations manage company-wide business processes, using a common database and shared management report tools. ERP software supports the efficient operation of business processes by integrating tasks related to sales, marketing, manufacturing, logistics, accounting and staffing throughout a business.” Based upon this definition, it is clear that VIVI PLC can gain many benefits from the implementation of an ERP system. After conducting a thorough review of the various ERP vendors, it is recommended that VIVI PLC should invest in SAP’s ERP system. Based on research conducted by Panorama Consulting Solutions (2018), out of the top four ERP vendors, SAP was identified as one of the most frequently selected ERP vendors in the ERP market, with a market share of 15% (see Figure 1). This is due to the fact that they offer ERP solutions which are appropriate for all business sizes.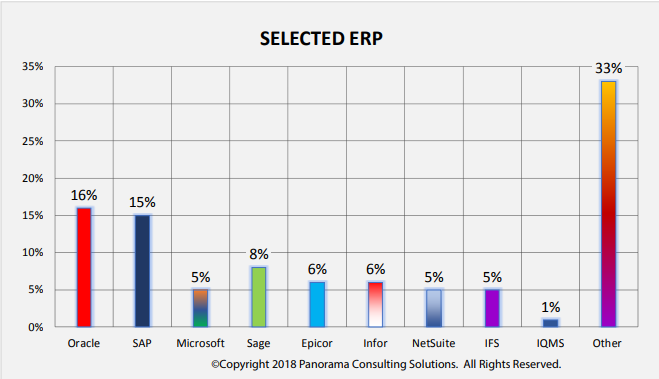
Supply Chain and Operational Benefits of ERP Systems
According to Monk and Wager (2013), the term supply chain describes all the activities that occur between the growing or mining of raw materials and the appearance of finished products on the store shelf. Furthermore, the functions within Supply Chain Management include developing production plans, ordering raw materials from suppliers, receiving the raw material into the facility, manufacturing products and shipping products to customers (Monk and Wager, 2013). Therefore, smoothing the sequencing of the processes in the creation of a product is significant in improving the end product and having overall business communication. Logistics, in particular, focuses on product distribution activities, while supply chain involves creation and obtaining of materials (Journal of Retailing, 2015). According to SupplyChainQuarterly (2011), company profits can rocket dramatically if costs are saved from the supply chain and logistics process. Annual savings can be as high as $2 million - $10 million depending on the size of the company (O'Byrne, 2011). As an electrical company, VIVI PLC could potentially gain benefits such as these and much more, which are outlined below.Integrated Systems and Streamlined Business Processes
The implementation of SAP’s ERP system can facilitate VIVI PLC’s aim to increase efficiency and streamline their current operations. SAP offers multiple modules which are designed for each business area such as, Sales & Marketing, Production and Finance. SAP’s Material Master Data is a central repository which contains descriptions of all materials than an organisation procures, produces and keeps in stock (SAP.com, n.d.). SAP’s Material Master Data can be used by VIVI PLC to integrate data from the sales, procurement, production, accounting and distribution departments (SAP, n.d.). This can give the company a single view of the supply chain data, therefore, lead to more efficient manufacturing operations, better inventory management and reduced cycle times. Thus, resulting in reduced costs (Partida, 2012). As shown in Figure 2, SAP’s Material Master Data integrates various data views.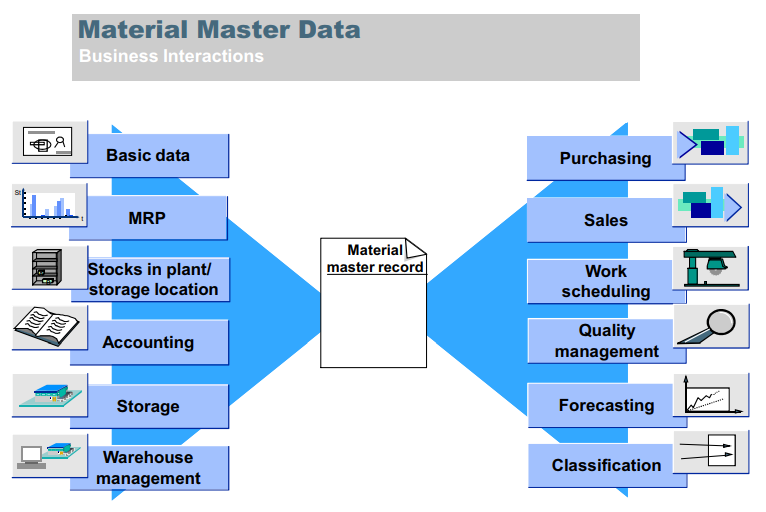
Figure 2: SAP Material Master Data Integrated Views (SAP, n.d.)
Here are examples of the information included in each view of the Material Master Data:
- BASIC DATA: Provides information such as the description, unit of measure, weight and volume of a particular material (see Figure 3).
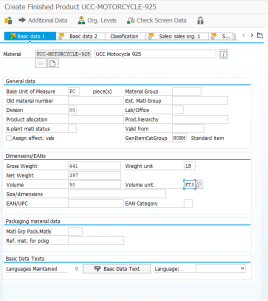
- MATERIALS REQUIREMENT PLANNING (MRP): As seen in Figure 4 below, information which can help with planning and inventory control for a certain material can be viewed. For example, planned delivery time, minimum safety stock and plant location. This information can be used by VIVI PLC’s procurement team to prevent over-purchasing & also by the production team to plan production based on the expected delivery time of the required materials.
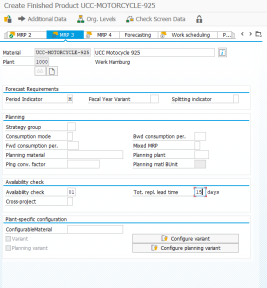
- ACCOUNTING & COSTING: Provides information in regard to the value and pricing calculations for a certain material (see Figure 5 below). For example, standard price (1,500.00) and future planned price (1,610.31). This information can be used by the accounting team at VIVI PLC when they are producing reports, this is important as Magal and Word (2012) state that “financial accounting is the ‘heart’ of the ERP system”.
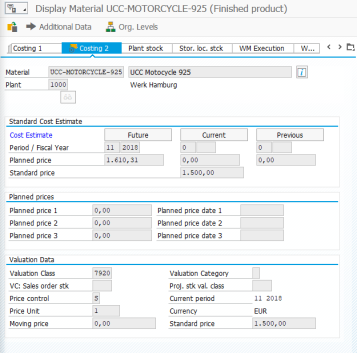
Improved Materials Management & Production Planning
VIVI PLC can use the Bill of Materials (BoM) and Routing documentation from SAP to help them improve their materials management and production planning operations. A Bill of Materials can be described as “the components that are necessary to produce a material” (Magal and Word, 2012). The Bill of Materials can be viewed as a hierarchy graphic (as seen in Figure 6) or a table of text, as seen in Figure 7. This information can be used by the manufacturing and procurement teams in the firm, so they can know the exact materials to order, how much to purchase and where to purchase the raw materials and parts from (Mandy, 2015).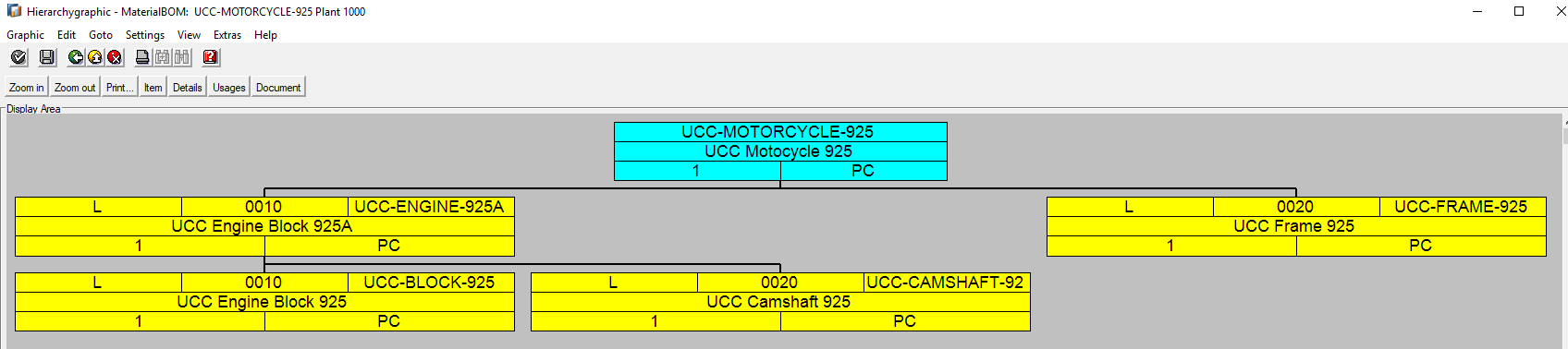
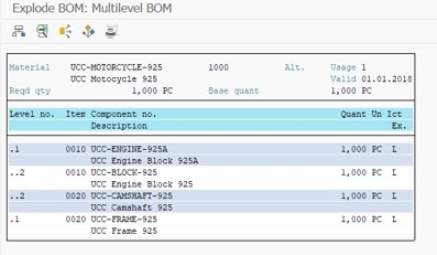
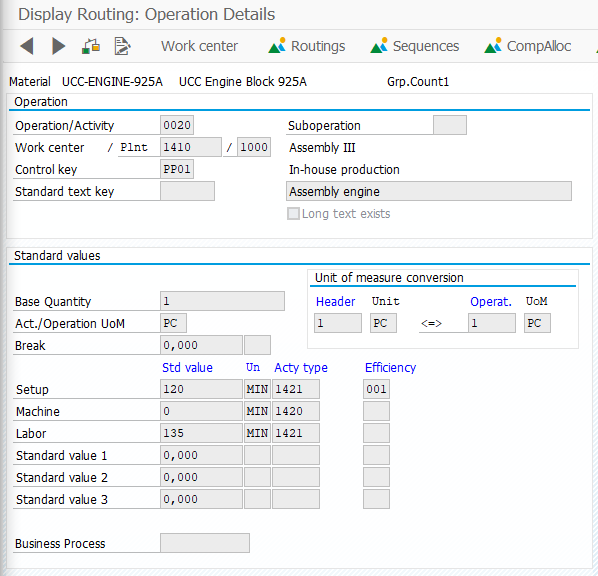
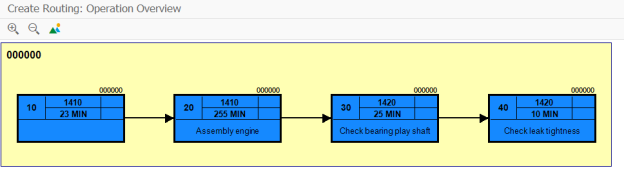
Automation of Processes
An ERP system will automate business operations, reduce manual input and eliminate repetitive processes (Workwise LLC, n.d.). SAP offers functionality which can be used to automatically calculate the cost estimate for a particular product based on the BoM and routing which was created previously. For example, once the Costing Data has been entered (see Figure 10), the cost of manufacturing a Motorcycle (£1,610.31) was automatically calculated (see Figure 11). This can help reduce the time taken for the accounting team at VIVI PLC to complete costing calculations as they are no longer required to manually calculate costs.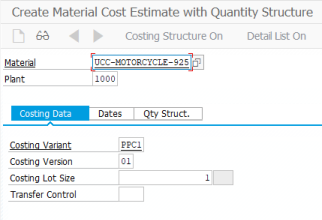
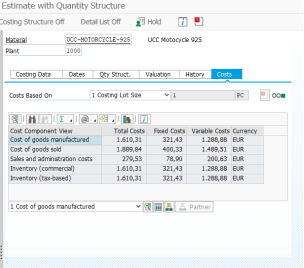
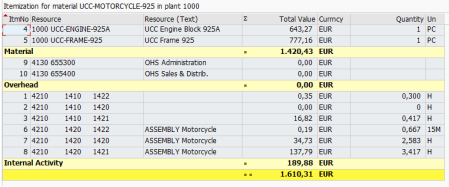
Supplier Integration
Supply chain management involves connecting a “company to other companies that supply the materials it needs to make its products” (Magal and Word, 2012). VIVI PLC. could improve supply chain visibility and reduce lead time for procuring materials from suppliers by sharing inventory and sales information via SAP’s ERP system. As seen in figure for Display Vendor Address and Purchasing Data, a Vendor Master Data document detailing information such as, the name, address, and terms of payment for VIVI PLC’s network of trusted suppliers can be created (SAP, n.d.). This information can also be maintained in a Source List (see Figure 14), which outlines which supplier a material can be procured from (SAP, n.d.). For example, as displayed in Figures 13 and 14, the assigned vendor number (e.g. 100540) shown in the source list for the raw materials, matches the approved vendor maintained in the Vendor Master Data. This can help the procurement team to control purchasing.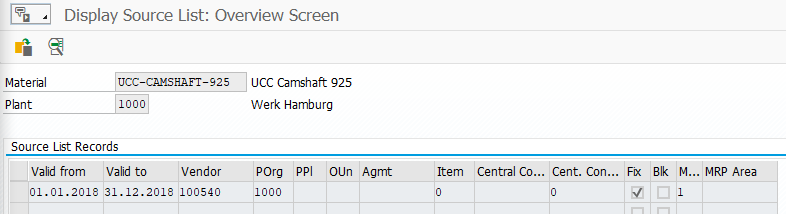
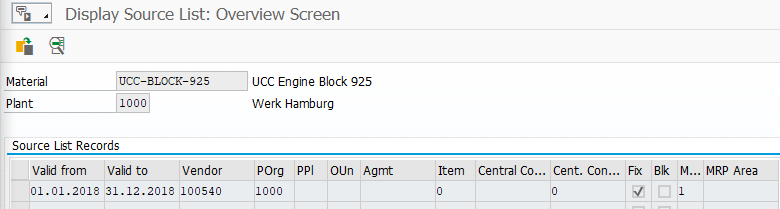
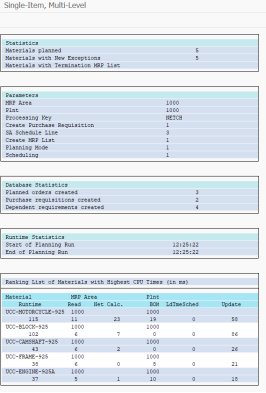
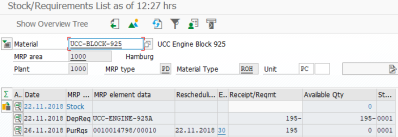
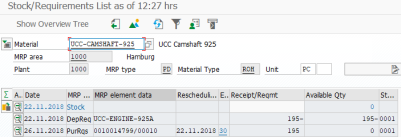
Reduced Inventory Held & Manufacturing Costs
According to Leão, (2015), an ERP system could potentially reduce inventory held by 20%, consequently reducing manufacturing costs by 5% to 10%. This can be achieved by adopting a just in time (JIT) system, using accurate and real-time inventory information produced from an MRP run. Thus, improving integration and communication with suppliers. JIT is an “inventory management system, used to manage the stock that is kept in storage. It involves receiving goods from suppliers as and when they are required, rather than carrying a large inventory at once” (Barlow, 2015). Companies who adopt a JIT system have a more cost-efficient method of holding stock (Barlow, 2015). For example, Dell reduced their inventory held from holding it from 20 – 25 days of inventory to having no warehouses whatsoever and no more than 2 hours of inventory being held in its factories (Breen, 2004). This is due to their efficient JIT inventory system and very good supplier integration (Breen, 2004). SAP’s ERP system can facilitate a JIT system as each time a sales order is entered (see Figure 17A), it can automatically trigger an MRP run (see Figure 18). This can enable VIVI PLC to share sales and inventory information with suppliers when required to meet demand rather than storing large volumes of raw materials and finished products.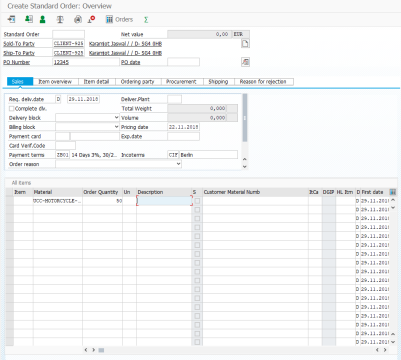
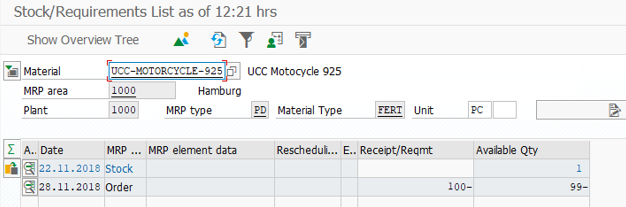
Improved Data Accuracy
Moreover, SAP offers functionality that can ensure that VIVI PLC’s stock level information is accurate and updated in real-time. As shown in Figure 19 and 20, a goods receipt document is created when goods are received at the warehouse from a supplier. The stock level is then automatically updated to include the quantity of the goods received.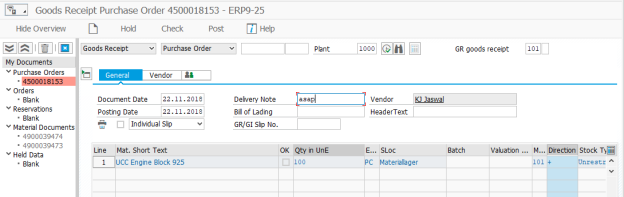
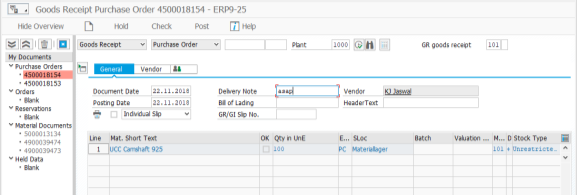
Potential Problems with ERP Implementations
While a successful ERP implementation can offer many benefits as discussed in Chapter 3, ERP implementation can also pose some challenges.Time & Ease of Integration
ERP implementations can be highly time-consuming. An example of integration failure is Hershey’s SAP implementation in 1999. They hastily invested into the SAP ERP system and it didn’t work in their favor. Despite being recommended an implementation time of 48 months, they demanded a 30-month turnaround. This resulted in the scheduling demands to coincide with one of their busiest periods. Hence, corners were cut in order to meet the scheduling demands, hence the overall implementation lacked. Consequently, Hershey’s was incapable of processing $100 million worth of Kiss and Jolly Rancher orders, even though it had most of the inventory in stock. This operational paralysis led to a 19% drop in quarterly profit and 8% decline in stock price (Ross, 2011). It is important to keep in mind that the application of an ERP system is made consistent across the whole business. Hence maintenance and communication are key. Therefore, there is a strong need for effective ERP system testing and implementation in order to mitigate exposure to the failure risks. Ross (2011) suggested that having the support, resources and long-term goals in place to maintain the unanimous decisions is key to a successful execution, along with backing from the top management.Cost/Budget
Research conducted by Panorama Consulting (2018) identifies that, a common reason for implementation failures, or in this case budget overruns, is not having eyes wide open as to where the cost and time dedicated to the project will arise (see Figure 21). A more realistic approach is to consider viable ERP solutions, flexible enough and scalable enough to support current and future growth, aligning with the organization’s business and IT strategies (Panorama Consulting, 2018).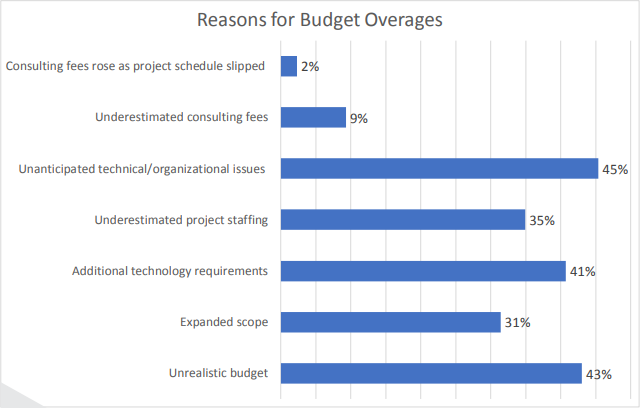
Limited Customisation
SAP offers multiple modules which can be integrated, however, it may be difficult to customize the system to meet VIVI PLC’s every business requirement. Too much customization adds risks as it could slow down the project and make it difficult to upgrade the system in the future (Rajesh, 2011). For example, Nike spent $400-million-dollars on implementing their ERP system, resulting in a $100-million-dollar loss in sales due to drops in demand forecasting and customization. There was a lack of testing and adaptation to changes (CNET, 2002). Hence, managing changes is significant to build employee trust and belief in business restructuring. Training, management, supervision and support can improve this.Change Management
VIVI PLC. is unfamiliar with the use of an SAP ERP system, therefore, there is a possibility that the change of systems may not be accepted by senior management and operational staff. This is because the organisational culture may change as a result of the new processes. The participation of users is very important for successful implementation of ERP projects (Rajesh, 2011). Hence, it is important that all employees including senior management are informed of the potential benefits to be realised through the successful implementation of SAP’s ERP system. Also, ERP systems can be difficult to learn and use (Rajesh, 2011), therefore user training should be carried out to ensure Global Widgets Plc. is able to effectively use the system implemented. In addition, processes and documents will need to be updated. Thus, it is advised that a strong project and change management team is formed to manage and support the ERP project throughout (Panorama Consulting Solutions, 2018).Conclusion
To conclude, based on the information discussed above, it is clear that VIVI PLC can gain many benefits both internally and externally through the implementation of SAP’s ERP system. VIVI PLC can improve operational processes and realise an agile and aligned supply chain (Lee, 2004), in order to respond quickly to meet demand and improve customer service. This can be achieved through an integrated system which can, encourage communication and collaboration between departments, improve the accuracy of information and improve relationships with suppliers. Thus, reducing the amount of inventory held and lead times, as well as, increasing efficiency and productivity. This is what VIVI PLC need as their current systems are not providing sufficient or accurate information, hence, implementing SAP’s ERP system will solve these problems.Bibliography
AWS, 2013. The Kellogg Company Case Study. [Online] Available at: https://aws.amazon.com/solutions/case-studies/kellogg-company/ [Accessed 28th Nov 2018]. Barlow, P., 2015. Just in Time (JIT) Advantages and Disadvantages. [Online] Available at: https://www.babington.co.uk/blog/accounting-blog/just-in-timeadvantages-and-disadvantages/ [Accessed 5th December 2018]. Breen, B., 2004. Living in Dell Time. [Online] Available at: http://www.fastcompany.com/51967/living-dell-time [Accessed 5th December 2018]. CNET, 2002. i2-Nike fallout a cautionary tale. [Online] Available at: https://www.cnet.com/uk/news/i2-nike-fallout-a-cautionary-tale/ [Accessed 27th Nov 2018]. Guru99, 2017. How to Create/Change/Display Routing in SAP PP. [Online] Available at: http://www.guru99.com/create-change-routing-sap-pp.html [Accessed 4th December 2018]. Journal of Retailing , 2015. The Role of Marketing Channels in Supply Chain Management. [Online] Available at: https://www.researchgate.net/publication/276212454_The_Role_of_Marketing_Channels_in_Supply_Chain_Management [Accessed 27th Nov 2018]. Leão, L., 2015. Reducing Inventory and More through ERP. [Online] Available at: http://www.cim-team.com.br/modern-electrical-engineeringblog/reducing-inventory-and-more-through-erp [Accessed 5th December 2018]. Lee, H. L., 2004. The triple-A supply chain. Harvard Business Review, October, 82(10). Magal, S. and Word, J. (2012). Integrated business processes with ERP systems. Hoboken, N.J: John Wiley & Sons. Mandy, 2015. Why a Bill of Materials is so important for manufacturing. [Online] Available at: https://www.unleashedsoftware.com/blog/why-a-bill-of-materials-is-soimportant-for-manufacturing [Accessed 4th December 2018]. Miller, N. (2016). National Grid Transmits Procurement to the Cloud with SAP Ariba Solutions. [online] Www2.deloitte.com. Available at: https://www2.deloitte.com/content/dam/Deloitte/global/Documents/Technology/gx-tech-national-grid-sap-ariba-june.pdf [Accessed 4 Dec. 2018]. Milner Browne. (2018). Serosep - Streamlining monthly reports with SAP Business One - Milner Browne. [online] Available at: https://www.milnerbrowne.com/case-study/using-sap-business-one-to-streamline-supply-chain-management/ [Accessed 5 Dec. 2018]. Monk, E. and Wagner, B. (2013). Concepts in enterprise resource planning. 4th ed. [S.l.]: Course Technology/Cengage Learning. O'Byrne, R., 2011. 7 ways everyone can cut supply chain costs. [Online] Available at: http://www.supplychainquarterly.com/topics/Strategy/scq201102seven/ [Accessed 27th Nov 2018] Partida, B., 2012. Material Master Data Management. [Online] Available at: https://www.apqc.org/blog/material-master-data-management [Accessed 27th Nov 2018]. Rajesh, K., 2011. Advantages & Disadvantages of ERP (Enterprise Resource Planning) Systems. [Online] Available at: http://www.excitingip.com/2010/advantages-disadvantages-of-erp-enterprise-resource-planning-systems/ [Accessed 27th Nov 2018]. Ross, J., 2011. A Case Study on Hershey's ERP Implementation Failure: The Importance of Testing and Scheduling. [Online] Available at: https://www.pemeco.com/a-case-study-on-hersheys-erp-implementation-failure-the-importance-of-testing-and-scheduling/ [Accessed 27th Nov 2018] Rouse, M., n.d. Bill of Materials (BoM). [Online] Available at: http://searchmanufacturingerp.techtarget.com/definition/bill-of-materialsBoM [Accessed 16 May 2017]. Rouse, M., n.d. Material Requirements Planning (MRP). [Online] Available at: http://searchmanufacturingerp.techtarget.com/definition/Materialrequirements-planning-MRP [Accessed 20 May 2017]. SAP, n.d. SAP Master Data: Materials Management. [Online] Available at: https://sapfidocz.files.wordpress.com/2013/06/62729459-sap-mm-master-data.pdf [Accessed 27th Nov 2018]. UPP, 2017. Kellogg's SAP Implementation Thrives with Upp Technology Enterprise Systems and Infrastructure Support. [Online] Available at: http://www.upp.com/it-staffing/case_studies/kelloggs_sap_implementation_thrives_upp_technology_enterprise_systems_and_in [Accessed 5th December 2018]. Workwise LLC, n.d. Top 15 Benefits of Implementing ERP Software. [Online] Available at: http://www.workwisellc.com/15-benefits-implementing-erp-software/ [Accessed 4th December 2018].
Cite This Work
To export a reference to this article please select a referencing style below: